In his article titled “Property and Casualty Insurance - To Repair or Replace”, Paul Haynes details adjustment considerations and common concerns that surface following many disaster events. Haynes starts out explaining that, “The basics surrounding repair versus replacement in a property and casualty insurance context seem pretty simple. Specifically, in a replacement cost policy, the insurer will pay the lesser of either the cost to repair the item or the cost to replace, new for old, without consideration of depreciation. The value would be limited to the actual amount expended to repair or replace the damaged equipment with comparable materials and quality.”
While this type of policy language is fairly standard, each loss has a unique set of circumstances, especially commercial losses, that tend to make what would otherwise be a straightforward adjustment, quite a bit more challenging.
Haynes goes on to say “Oftentimes the repair option is the most likely course of action. However, other factors must also be considered, such as any applicable code requirements and/or the cost/benefit of repairing older equipment such as computers. The question is whether it is possible to repair outdated, inefficient equipment of similar quality in today's market. Further, what if the insured had plans prior to the loss to replace or upgrade the equipment, and who bears the burden to prove that the damaged property is repairable?”
Additionally, “If the insured has claim for a business income loss and or extra expense, the additional costs associated with an extended period of restoration must be weighed against the cost of replacement.”
Haynes concludes his article by stating that “Anything can be repaired; it's just a matter of how much reserve engineering you want to put into it. However, if you are considering paying repair costs, be prepared for a variety of potential challenges.”
Haynes raises legitimate concerns that on the surface appear to apply to any loss. When considering personal lines, habitational, and even light commercial claims, the likelihood of replacement equipment existing on a suppliers’ shelf are quite high. A cost benefit analysis of decontamination followed by testing and repair (by certified manufacturer representatives), should be performed.
Commercial losses, such as those that occur in manufacturing facilities, medical centers, and computer server farms, introduce custom equipment configuration variables that make the repair versus replacement cost analysis much more complex.
Let’s breakdown Haynes’ noted concerns and attempt to address the questions from a commercial loss point of view:
- Factors must also be considered such as any applicable code requirements and/or the cost/benefit of repairing older equipment such as computers. In a commercial setting, an older computer may be controlling manufacturing machinery. Replacement of the computer will likely cause communication problems, as the old machine controllers are still programmed with software that was designed to communicate with computer operating systems of that same generation. Restoration, which will be defined as decontamination followed by testing, repair and recalibration moving forward, is the fastest and most economical way to get the entire machine back in production. It is possible to restore outdated inefficient equipment. Replacement parts, if needed, would have to be obtained from another computer of the same generation.
- Who bears the burden to prove that the damaged property is repairable? Generally speaking, equipment owners do not know how to efficiently recover from a loss. They are dependent on their trusted advisors, usually the insurance agents and/or the equipment manufacturers, when submitting their proof of loss and overall claim. Since most loss adjusters are not equipment specialists, they rely on those that are able to detail the available options. Simply put, equipment owners often submit claims for wholesale replacement, because they do not have experience with other recovery options. Insurance carriers on the other hand, that do have experience with similar losses, would then have to basically prove, if we are going by the language in the question above, that other means of recovery are viable options as well. They do so by introducing companies that specialize in post loss recovery and allowing those companies to present their expertise.
At this point, repeatable science and practices that settle claims are critical to appreciate. Let’s set the stage with the following: Recommending a recovery path by providing the equipment owner, and their representatives, scientific data that can be reproduced by anyone, as well as options that minimize their business downtime, will help all parties reach a claim settlement that much faster.
A disaster event can cause contaminants to settle on highly sensitive electronic components and mechanical assemblies. Depending on the type of loss, the contamination effects can vary widely. One thing that remains constant is that if the contamination is not properly quantified and restoration is not properly explained, the equipment owners, and their trusted advisors, will claim a solution that fits within the purview of their expertise.
Harvesting wipe samples and mapping the facility with analytical results, sets the stage for a meaningful conversation about recovery. This is the first step in the “burden of proof”. Empirical data provides contamination danger visibility that eliminates hypothetical conversations.
Repeatable science means that anyone should be able to harvest samples in the same general location, using the same type of collection media and storage container, and the results will be very close. The reason the results will not match 100 percent is because soot does not necessarily settle on surfaces uniformly and pre-existing debris can vary as well. Therefore, analytical testing will quantify which areas of the facility sustained higher or lower levels of exposure, and which may not have been exposed to anything. Samples harvested from a newly manufactured circuit board, before it is cleaned, will show elevated levels of manufacturing by-product that has to be removed for quality assurance purposes. Once removed, testing for cleanliness again and comparing to an industry standard, is the normal quality assurance practice. The same protocols should be observed in the field following a disaster.
It is good practice to engage the original equipment manufacturers (OEM’s) or third-party service providers that serve an important role in the recovery process. Getting the manufacturers the data they need to be able to compare to the industry standards helps instill certainty in the process. This is all part of the burden of proof. Every entity that backs equipment with a service contract or warranty, needs to be assured that loss related contaminants were effectively removed and proven so with repeatable science.
By the Numbers
The Department of Energy (DOE) published a fire protection handbook that included a study on equipment failure probability after smoke exposure. The study provided scientific data regarding corrosive contaminant levels, below which the probability of failure is effectively zero and also levels above which restoration may not be a viable option depending on surface degradation such as pitting. A graphical representation of the DOE study is shown below.
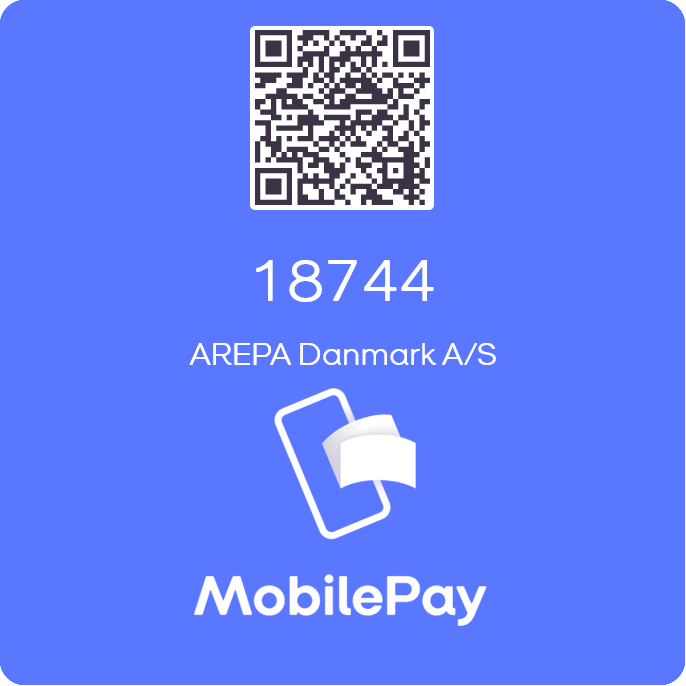
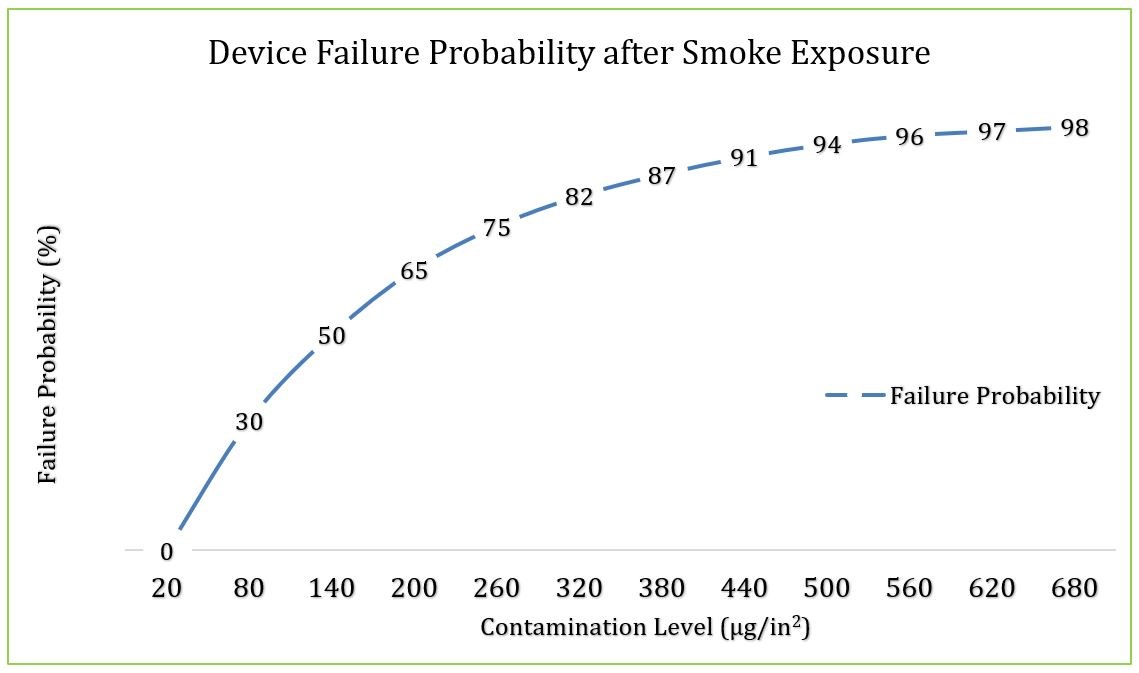
DOE Fire Protection Handbook, Volume II
As exhibited in the graph above, the DOE study shows that equipment with contamination levels that exceed 500 µg/in2 (micrograms per square inch) of aggregate chloride equivalent (Cl), will experience higher rates of failure if the equipment resumes production prior to removal of the corrosive matter. The study also shows that at contamination levels of 20 µg/in2 or less, the probability of failure is effectively zero. Therefore, based on the DOE study, for restoration to be successful, the level of corrosive particulate must be reduced to below 20 µg/in2.
While conforming to a study is better than not having anything to compare results to, it is ideal to measure contamination levels the same way manufactures do. For electronic assemblies containing printed circuit boards (PCBs), the IPC J-Standard should be adhered to. Founded in 1957, the Association Connecting Electronics Industries is accredited by the American National Standards Institute (ANSI) as a standards developing organization. The J-Standard is titled “Requirements for Soldered Electrical and Electronic Assemblies” and is recognized as the sole industry-consensus standard for soldering processes and materials. The standard sets a post decontamination threshold level of 10.6µg/in² of aggregate sodium chloride equivalent (NaCl), as the acceptable cleanliness threshold for newly manufactured boards. Certified IPC Specialists (CIS) are trained to meet post assembly acceptance standards used to ensure electronic assemblies meet acceptance requirements for the electronic industry.
The Importance of Analytical Testing
To ensure that equipment decontamination is successful (e.g. meets the IPC standard), analytical testing is vital. Perhaps we should take one step back and clarify that it is just as vital to quantify the contamination during the initial site assessment, to determine which pieces may not require decontamination at all. Empirically quantifying that equipment was not exposed will help owners resume some level of production.
Therefore, samples should be harvested at the start of the recovery process, as part of the assessment and triage, to establish a baseline of contamination. It is actually common for testing to show that some equipment was not affected, and those items can potentially be put back into service as soon as the facility mitigation is complete.
Pre-recovery sampling also shows which items may require preservation. Preserving equipment with a rust inhibitor will help save surfaces that would otherwise corrode if not addressed shortly after exposure. Rust can cause irreversible surface damage.
Samples are then harvested again after the equipment has been decontaminated. During this step, empirical data will show if the decontamination was successful. The results should be shared with manufacturers to prove that contaminants were thoroughly removed and it is safe to power the equipment on for testing.
What Tests are Performed?
Wipe samples are used to identify ionic species. AREPA tests for both Anions, such as Chlorides, Sulfates and Nitrates, as well as Cations such as Sodium, Magnesium and Calcium. The lab utilizes the data to calculate the aggregate chloride equivalent (compared to the DOE study) as well as sodium chloride equivalent (compared to the IPC J-Standard).
Conductivity and equivalent salt density testing can help with initial equipment triage as well as post decontamination surface checks. This type of testing is not a substitute for analytical testing for two reasons. The first is that the results cannot be compared to the IPC standard threshold (10.06 µg/in2 or 1.56 µg/cm2). The second is that these instruments typically measure only soluble salts. While the contamination may be visible, if it does not adhere to the sample media, the result will be inaccurate. Therefore, harvesting samples and having them processed in a lab yields results that manufactures accept as valid proof that contaminants were properly removed.
Summary
Employing repeatable science instills certainty. Owners need to be assured that equipment will operate as it did before the loss event, manufacturers need evidence that contaminants will not cause equipment failures beyond those expected as part of normal operation, and professional equipment decontamination firms need to be able to place their warranties with confidence.
As noted above, in many cases empirical data will prove that decontamination is not necessary at all. For this reason, some firms do not perform such testing. With a team of IPC certified specialists, AREPA is proud to be among assembly process engineers, quality assurance professionals, and others responsible for the quality and reliability of soldered electronic assemblies. Meaningful data, in additional to a transparent collaboration with manufacturers and service providers, leads to buy-in. All parties agreeing on a path forward helps settle claims that much faster.
To find out more about how a lack of testing and immediate mitigation can lead to corrosion and further problems, check out our on demand webinar on corrosion*. Then, contact us to find out how we can help you recover from (or plan for) a loss event.
*Please note: on demand webinars are not applicable for continuing education credits.
ABOUT THE AUTHOR
By: Mark Lerche
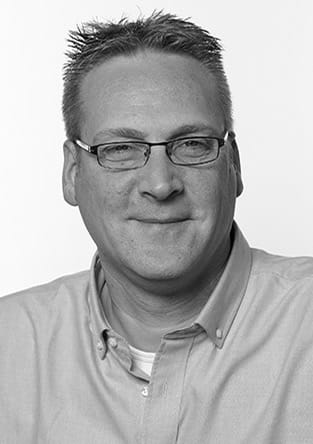
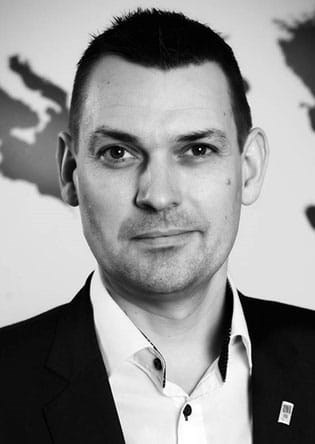
Mark joined the AREPA team in December of 2020 as Regional Sales Manager for the Nordics. In this role, Mark is responsible for managing the overall sales efforts for AREPA in the Nordic region supporting the efforts and strategy of the global sales team.