A fire is one of a business owner’s worst nightmares. Business interruption, lost production as well as building and equipment damage are now top of mind in addition to having to manage client expectations to ensure they do not revoke orders and take their business elsewhere.
When we envision fire damage, we typically think about equipment that was exposed to elevated heat, fire extinguishing activities (water, ABC powder, wet chemical, foam, dry chemical), and physical impact from a compromised structure. Unless the fire consumed the entire building, this type of catastrophic event will be somewhat localized in or around the area of origin. Areas further out may have been exposed to varying levels of soot or perhaps nothing at all.
Invisible Exposure That Can Lead to Damage
In an effort to understand what could exist on a surface that would be considered “invisible”, it is important to characterize smoke and why some fire events generate more smoke than others.
Smoke is comprised of small solid, liquid and gas particles. During complete combustion, everything is burned or consumed, producing just carbon dioxide and water. Because the air we breathe is made up of only 21 percent oxygen, a large volume of air is required for complete combustion to take place.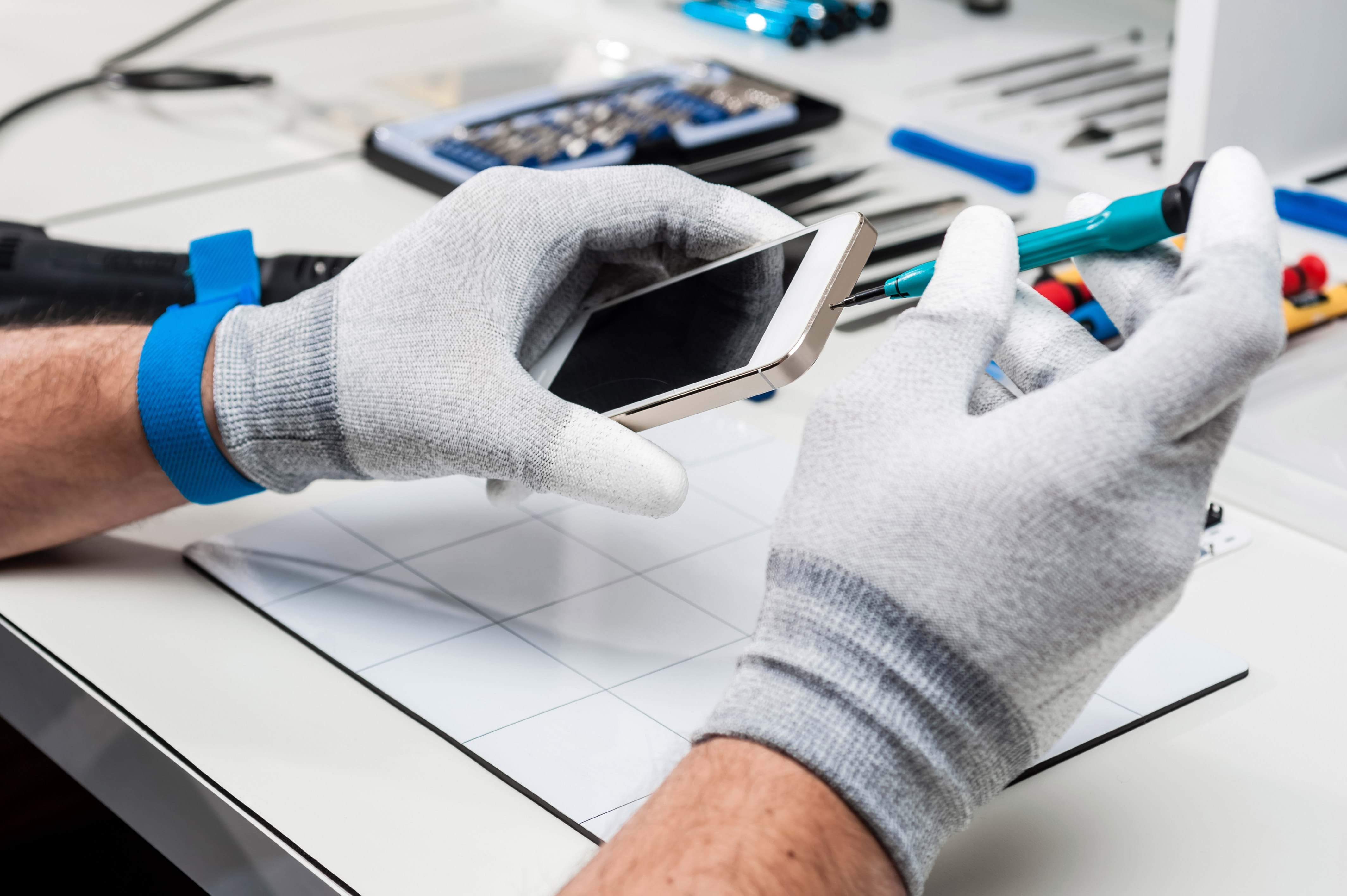
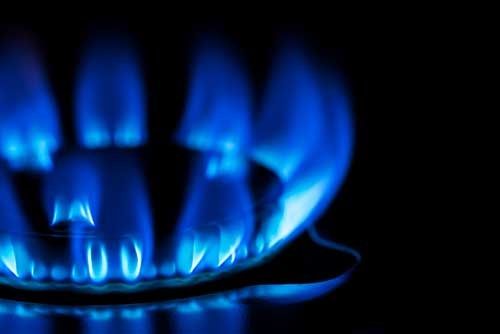
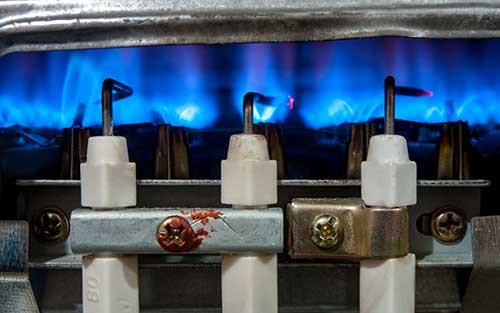
Images exhibiting blue flames from complete combustion
While smoke may contain different chemicals, visible smoke is mostly carbon (soot), tar, oils and ash. Smoke is observed when there is incomplete combustion, which translates to insufficient oxygen to burn the fuel (or consumed materials) completely. When we witness incomplete combustion, not everything is burnt. Smoke is therefore a collection of small unburned particles. Individual particles are too small to see with the naked eye, i.e. invisible, although when grouped in larger quantities, we view them as smoke.
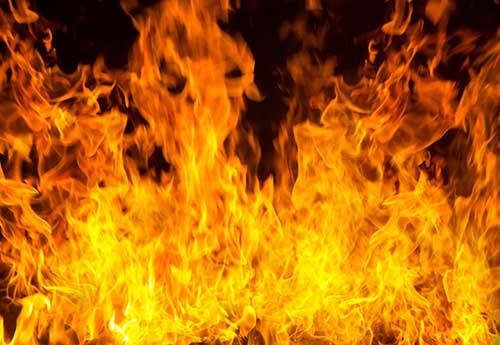
Incomplete combustion is characterized by an orange colored flame
What’s the difference between smoke and soot? As discuss above, smoke is a super-heated aerosol that is comprised of gases, vapors and particles. Whether mitigating the facility or equipment, no one is remediating smoke, because if you can see smoke, the area is either still on fire or shortly after extinguishing. That is not a healthy environment conducive for recovery activities. Soot, on the other hand, is a product or residue that is created from a carbon organic and/or inorganic based substance, in addition to some chemicals, left over after smoke dissipates. It is a product of incomplete combustion (see photo above).
Smoke and soot can spread to areas of the facility not directly affected by the fire, depositing products of incomplete combustion on highly sensitive equipment. Depending on what was consumed in the fire, the soot residue may not be obvious to the naked eye. In a clean office environment, foreign matter will stand out. In a manufacturing environment, soot residue can blend in with the normal production by-product or environmental debris. Therefore, in many cases, soot may not be immediately visible, although it will eventually make itself known in the form of corrosion (or rust on iron substances), which will deteriorate the surface it settled on. If not properly addressed, a susceptible metal will form pitting, a localized breakdown of metal that manifests in small cavities or pits. This type of damage cannot be reversed.
Contamination should be quantified as quickly as possible after a fire. By identifying the composition of the settled contaminants, a determination can be made about areas of a facility that may not require any action and can resume production safely, versus areas that were impacted. For areas with loss-related contaminants, quantifying the composition provides a triage mechanism. Equipment with elevated levels of corrosive matter would have to be addressed before those with less urgent levels. A restoration expert can help determine what equipment has been contaminated, and the best course of action to restore the equipment and get the business back in production.
How Extinguishing the Fire Can Affect Equipment
If your facility has a sprinkler system, there’s a good chance that it was activated to extinguish the fire. The fire department will use their extinguishing methods as well, whether via water, foam, or a non-water-based suppression system, which could be viewed as “favorable” in computer server rooms as an example. The reason “favorable” is in quotation marks is because many data centers favor clean agent (gaseous) suppression systems that do not leave a chemical residue on the equipment.
Once equipment is wet, hopes for resumption of business increase as the facility and equipment are dried. Some business owners even attempt to power on equipment just to gauge the functional status. Drying everything, while a reasonable first step, does not remove settled contaminants that have potentially reached the inside of sensitive equipment.
An activated sprinkler system can also temporarily raise the humidity in the facility. Combined with other extinguishing measures that may leave residue on the equipment, this scenario can cause corrosion to form on vulnerable electronic components and metal surfaces. Corrosion, or dried water residue that has yet to cause corrosion, may not always be apparent at first. While it does not require a large amount of conductive contaminants to cause an electrical short circuit, a sizable amount would have to blanket circuitry to cause overheating. It is critical to contact a professional restoration firm as soon as possible to perform proper analysis and decontamination.
Environmental Changes
As mentioned above, an activated sprinkler system can elevate the humidity in the facility. Fire damage can also cause other environmental changes. For example, affected areas may be left open to the outside elements, causing variations in humidity and temperature that can further stress affected equipment. Controlling the environment is the first step to a successful recovery. Erecting barriers to protect the equipment from a breached section of the facility, will minimize cross contamination and allow professionals to place dehumidifier to lower the relative humidity.
Equipment Stabilization After a Fire
It's important to protect the environment around your equipment and get it stable as quickly as possible.
The first rule of equipment stabilization is not to power anything on until it has been fully inspected. Powering on equipment that is contaminated can result further damage, and it can potentially be the catalyst for another fire. Therefore, do not turn on equipment even if it’s just for testing purposes.
While it is important to call a restoration expert immediately following an incident, there are measures that can be employed independently in an effort to mitigate the loss. For instance, applying water displacing lubricants that inhibit rust. When deterioration of metal surfaces is apparent, applying a thin layer of a rust inhibiting lubricant will minimize surface deterioration. There are also vapor phase corrosion inhibitors (VPI) that create a barrier layer to protector contaminated electronics.
Proper stabilization and preservation measures will slow equipment deterioration. In fact, it can make the difference between being able to restore your contaminated equipment and having to replace it.
Preparing for Restoration Experts to Assess the Damage
Depending on the facility and severity of the fire, your restoration expert may provide additional suggestions in an effort to protect the affected equipment. While there are businesses that are self-insured, many companies will consult with their insurance carrier, or assigned independent adjuster, before committing to work both on the facility and its content. As such, the time window between the day the loss occurred and the date at which adjusting decisions are made can make a difference in equipment recoverability if environmental stabilization and equipment preservation are delayed.
Tips to prepare for the arrival of the restoration experts to assess the damage:
- Disconnect the electricity supply to equipment, including uninterrupted power supply (UPS) systems.
- Remove excess water by mopping or wiping. ‘Wet-type’ vacuum cleaners can be used for removing large quantities of water from widespread areas. Do not forget to remove water under raised floors and in electrical ducts.
- Place barriers to prevent cross contamination in various building zones at entry ways.
- Install dehumidifiers in the areas where the affected equipment is located, and reduce the humidity to below 40 percent RH. If dehumidifies are not available, use fans to circulate air through the affected areas.
- Make sure that the area is safe to enter. If the building is damaged, this may involve having an engineer check structural integrity.
- Determine whether there are any asbestos concerns to ensure proper PPE is utilized.
- If available, have an equipment inventory list available digitally or via hard copy.
- If the equipment is backed by a warranty or service contractor, scheduling the manufacturer or third-party service provider to beat the site during the inspection, will help ensure everyone is on the same page.
Equipment restoration is usually a much more cost-effective and faster alternative to replacement. If you experienced a fire or other incident, you need restoration experts who can help you get up and running as quickly as possible. Download our brochure to find out what AREPA can do for you, or contact us to get more information and the expert help you need.
ABOUT THE AUTHOR
By: Soren Duelund Sorensen
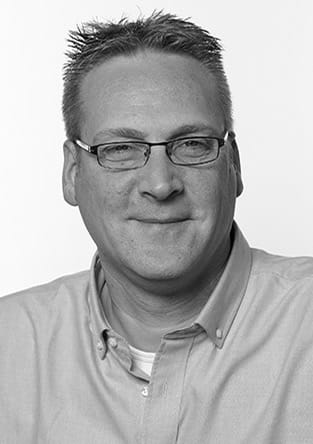
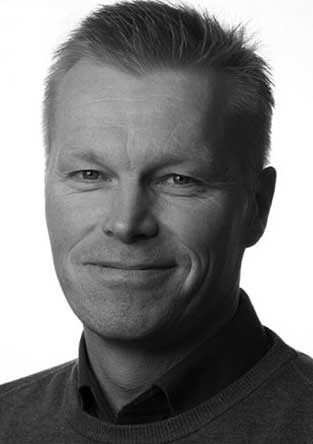
Søren is a mechanical engineer with experience performing damage assessment to high-tech electronic, electrical, and mechanical equipment that was impacted as a result of fire, water or other contamination event. Søren has conducted hundreds of accurate and in-depth equipment inspections to determine extent of damage, repair/restoration, and potential cost-effective solutions to mitigate business interruption. He has project managed the decontamination, testing, and repair, which includes working directly with the equipment owners, their technical representatives, and the manufacturers to successfully resolve equipment loss claims.