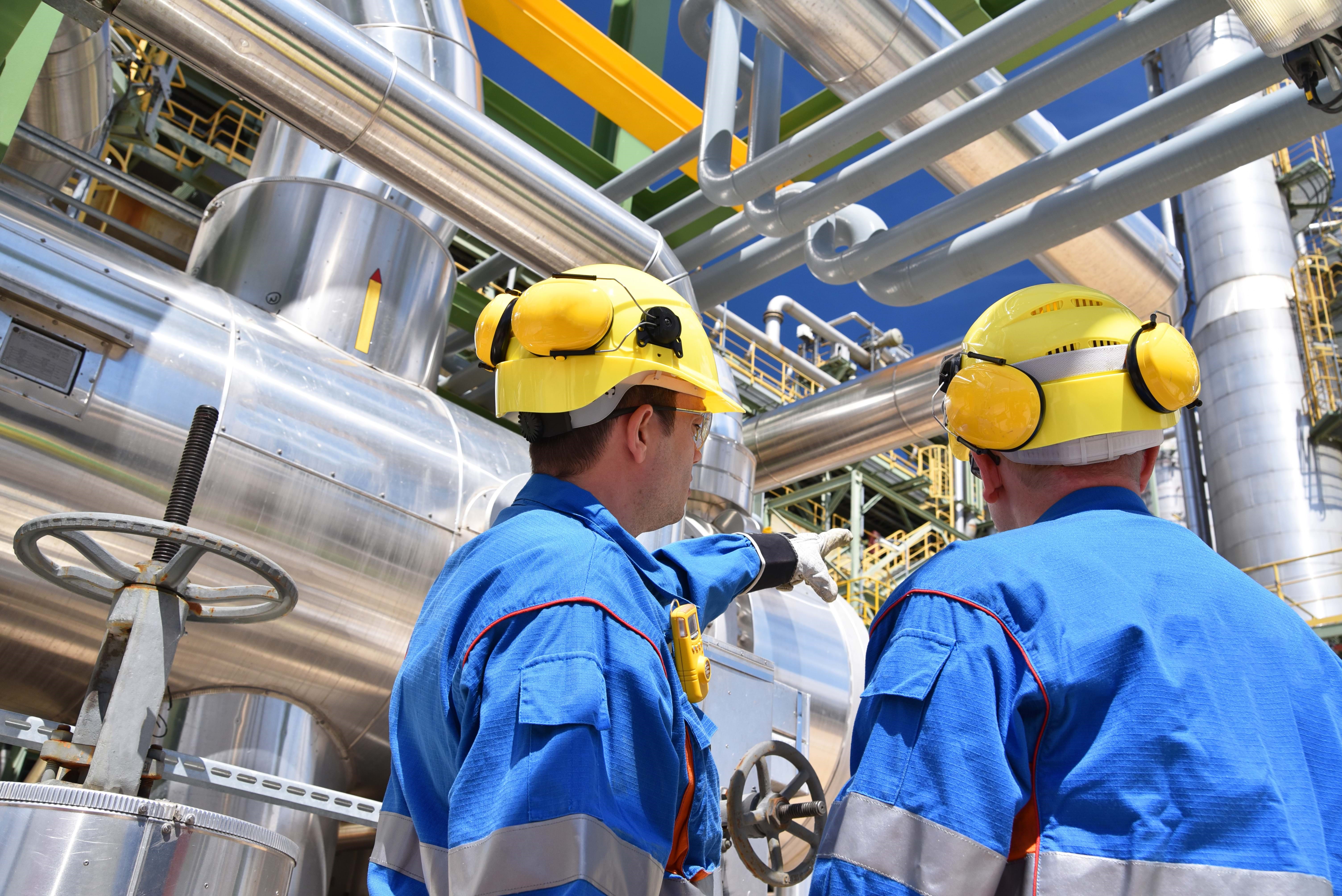
Effectively maintaining and servicing business critical equipment is critical for all stakeholders.
Effective preventive reconditioning of your machines and other business-critical equipment is of great importance for the continuity of your business operations. Find out what preventive reconditioning is, why it's important, and how AREPA can help your business do just that. In this article we answer questions such as:
- What is preventive maintenance?
- Why is preventive maintenance necessary?
- The 5 Benefits of Preventive Maintenance
- Tips for a Preventive Maintenance Plan
- Types of Preventive Maintenance Plans
- What can AREPA do for you?
- What qualifies for preventive reconditioning?
What is preventive maintenance?
Over time, pollution in and on your machines and installations can cause failures or downtime. Preventive maintenance or reconditioning is used to prevent defects and/or malfunctions due to contamination of machines and technical installations before they happen. AREPA specialists can help increase productivity, reliability, and the overall life cycle of the machine or equipment through preventive maintenance.
Why is preventive maintenance necessary?
By applying routine preventive maintenance, particularly technical reconditioning (cleaning the contamination that can lead to malfunctions), you prevent technical installations from failing and thus causing unnecessary operating downtime, which endangers your continuity. In addition, you increase the reliability of your machinery, reduce the chance of repair costs, and ensure minimum downtime. But there are more advantages to preventive cleaning of your machines and installations.
The 5 Benefits of Preventive Maintenance
Preventive cleaning of your industrial machines and installations provides you with five major benefits.
- Preventive maintenance dramatically reduces the risk of machine breakdowns
- Occupational safety increases for the employees who work with the machines
- There are no significant repair costs, because the machine is constantly kept in good condition
- The continuity of your business is guaranteed and downtime is minimized
- Preventive maintenance increases the reliability of your machinery
Tips for a Preventive Maintenance Plan
We record how preventive maintenance is carried out in a maintenance plan. By drawing up a maintenance plan, incipient contamination quickly comes to light. AREPA is happy to collaborate with you on the plan. In any case, there are six rules of thumb that you can keep in mind.
- Let an AREPA technical specialist review your maintenance plan to ensure that you don't miss anything. This specialist can identify contamination risks through analyses and is well aware of the possible consequences of not carrying out preventive cleaning.
- Map out your machinery and installations. Which machines and systems are absolutely important for your business activities? Place it at the top of the list.
- Gain insight into the risk-sensitive points of each machine and installation. Here, too, AREPA can play a proactive role. This clarifies where most attention should be paid during the preventive cleaning process.
- Describe how you can apply preventive maintenance to prevent the most common malfunctions for each machine and plant component.
- Write down the desired action per machine and installation. AREPA can contribute to the cleaning of the machines if desired.
- Ensure that the right technical specialists are aware of the desired action(s) in time.
The Types of Preventive Maintenance Plans
You can implement several types of maintenance plans to maintain and optimize their equipment and systems. The type of maintenance plan you choose depends on the equipment and machinery for which the plan is intended. In all cases, preventive reconditioning can be part of the maintenance package you choose.
Time-based maintenance
With a time-based maintenance plan, maintenance is scheduled at fixed time intervals, such as every year, every six months, or every month. This maintenance plan uses preventative reconditioning and replaces parts that may have shown wear and tear. An example of time-based maintenance is the annual inspection and maintenance of an HVAC system to maintain air quality and optimize equipment efficiency.
Condition-based maintenance
This type of maintenance plan is based on monitoring the condition of the equipment. Maintenance is only carried out when necessary. For example, if a machine shows vibrations that exceed a certain threshold. This may indicate problems with the bearings. Applying preventative maintenance, such as replacing the bearings before they fail completely or removing debris, can keep the equipment running efficiently and prevent downtime.
Predictive maintenance
Predictive maintenance is an advanced maintenance strategy that uses data analytics and machine learning to predict the condition of equipment and anticipate possible future failures. For example, a machine that slows down may indicate a possible defect in the engine. Implementing preventative maintenance, such as replacing the engine before it fails completely, can help prevent downtime and maximize equipment efficiency.
Run-to-failure maintenance
This type of maintenance plan does not carry out preventive maintenance. Instead, the equipment is only repaired when it fails. This can be efficient for equipment that has little impact on operations and is relatively inexpensive to replace or repair. However, if the equipment is critical to operations, the run-to-failure maintenance can lead to high repair costs and downtime.
What can AREPA do for you?
At AREPA, we perform preventive maintenance on all technical equipment. We’re the experts you need when vital equipment and systems are damaged, and based on our long experience with repairing and restoring technical equipment after damages, we also have a depth of experience advising company personnel on best practices for maintaining equipment and preventing premature equipment failures or obsolescence.
Over 40 years of experience
Thanks to our more than 40 years of experience in the field of technical reconditioning of equipment all over the world, we use the best and latest methods. In addition, we provide sound advice to prevent malfunctions or failures of your equipment. Our services in this area are broad but can be customized to any businesses’ needs. At a minimum, all AREPA Preventive Maintenance services include an overall assessment and evaluation of the equipment’s current condition, as well as suggestions for improvements to equipment operations and performance.
What qualifies for preventive reconditioning?
Arepa's technical specialists have extensive experience in preventive cleaning of machines, equipment, and installations such as:
- Business Critical Equipment
- Electrical Cabinets and Controls
- Equipment/systems prone to environmental/manufacturing byproducts (i.e., dust, humidity)
- Process Equipment
- Server Rooms
- Frequency Drives
- High Voltage Installations
- Transformers
- Automation Systems
- CNC Machines
We are happy to work with you!
Curious about what we can do for the periodic cleaning of your machines or technical installations? Our specialists are happy to think alongside of you! Contact us at +47 920 15 900 or fill in the form below, and we will contact you as soon as possible.